SWaP-optimized mission systems for unmanned platforms help expand capabilities
StoryMarch 13, 2024
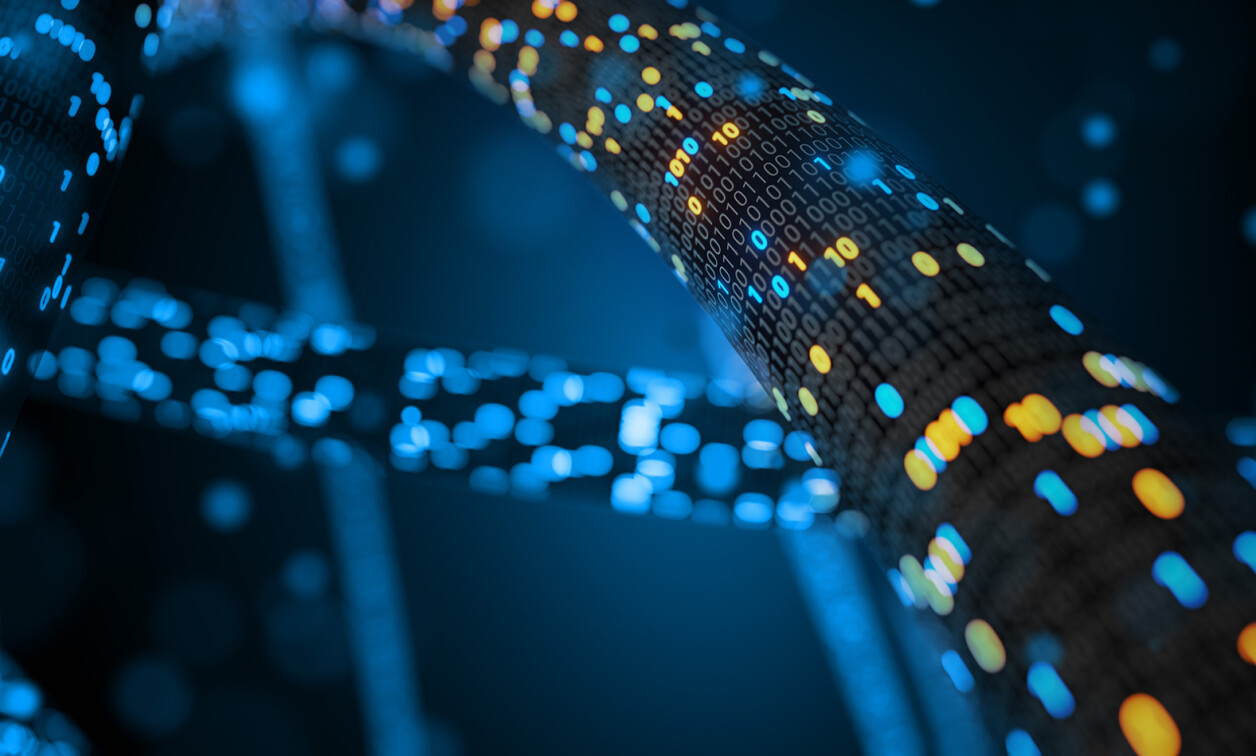
Aerospace and defense systems integrators continue to push for reductions in size, weight, power, and cost (SWaP-C) to support advanced sensor/vetronics payloads onboard unmanned reusable and attritable platforms. Fortunately, advances in the miniaturization of mission-processor and network-switch subsystems are enabling designers of UAS (unmanned aerial system), UGV (unmanned ground vehicle), UUV (unmanned undersea vehicle), and USV (unmanned surface vehicle) platforms to expand their mission capabilities.
What constitutes optimal size, weight, and power (SWaP) specs for a particular electronics LRU [line-replaceable unit] varies greatly depending on the target platform and application. SWaP goals for unmanned aerial system (UAS) platforms, whether military or commercial, are typically dictated by the size of the payload that a platform can carry. The platform’s mission is often driven by the capabilities brought by the payload. For example, in contrast to small commercial UASs, consider a military high-altitude/long-endurance (HALE) platform that can carry 1,000 pounds (approximately 450 kg) of payload electronics and are often used for persistent intelligence, surveillance, and reconnaissance (ISR) use cases.
In comparison, the small commercial UAS more typically will have payload capability of a few pounds or less. Designers of these systems may be satisfied to get an HD [high-definition] camera onboard a UAS that flies for only about 30 minutes due to the limitations of the aircraft’s battery. For such small platforms, both airborne and ground, micro-miniaturization of systems becomes very desirable. Systems integrators often look at the operational and logistical impact of the electronics that are added to an aircraft or vehicle platform, with some UAS suppliers going so far as to break down the cost of every pound (or kilogram) of payload weight in terms of cost-per-pound/kilo. Shrinking the physical size and weight of payload electronics not only delivers cost savings, but it also provides the ability to add more sensors and C4ISR [command, control, communications,computers, intelligence, surveillance, and reconnaissance] equipment to enhance operational mission capabilities for the end user.
To further illustrate how much SWaP impacts platform cost, consider three numbers: 1, 30, and 60: As a data point, one major North American UAS supplier has calculated that for every one (1) pound of weight they can eliminate from their UAS platform dedicated to ISR missions, they save approximately $30,000 in operational cost for the vehicle. For their combat UAS platform, they save even more, approximately $60,000 per pound.
In addition to cost impact, SWaP can affect feasibility for implementing mission capabilities. A major U.S. Army tactical UAS underwent a tech refresh to add an onboard network backbone, involving the integration of a fully managed Ethernet switch. Launched from a trailer-mounted pneumatic catapult and used for reconnaissance, surveillance, and targeting applications, this particular UAS has a rather small airframe and payload bay. The integrator performed a volumetric analysis and determined that the size available for a network switch LRU was limited to roughly the size of a pack of playing cards and about half a pound in weight.
Since the electronics payload area wasn’t generous in size, if a switch could not be found to meet this form-factor requirement, the UAS would have been unable to add the desired network readiness capability. This would likely diminish situational awareness and potentially lead to a costly redesign, since the switch was intended to link an onboard video encoder, mission processor, and warfighter communications devices via a common Ethernet network.
The miniature Ethernet switch has since been broadly deployed in not only UAS platforms, but also on far larger fighter-aircraft ISR sensor pods, helicopter sonar dipping systems, autonomous submarine networks, tactical ground vehicles, unmanned rotorcraft, and dozens of other SWaP- constrained platforms. The switch’s wide adoption is a testament to the need for ultra-small-form-factor (USFF) devices and the diverse applications that benefit from them; whether the platform is very small or much larger, low SWaP is advantageous.
Making it miniature
In large part, the miniaturization of electronics is made possible by advancements in commercial technology. Three notable enablers in this regard include system-on-chip (SoC) technology, intelligent power-management technologies, and mechanical component miniaturization. Semiconductor devices for computing and networking are more energy-efficient than ever before and are evolving to include more functionality in the same physical packaging. With fewer discrete components to integrate, printed circuit board assemblies (PCBAs) can be smaller. Traditional system architecture might have previously factored in multiple separate components, whereas today system designers have SoC alternatives that combine processing, memory, other controllers, interfaces, and physical transceivers all in a single chip.
In the case of the USFF Parvus DuraNET 20-11 20-port Gigabit Ethernet switch (Figure 1), its integrated switch SoC includes not only a nonblocking Ethernet switch fabric, but also a MIPS processor (for management), fully integrated copper PHYs (physical transceivers), DDR memory controller, and IEEE-1588 precision timing protocol (PTP) controller for accurate time stamping. This style of SoC approach has enabled the miniaturization of military electronics, particularly for low to mid-power devices.
[Figure 1 ǀ The USFF Parvus DuraNET 20-11 20-port Gigabit Ethernet switch SoC combines processing, memory, other controllers, interfaces, and physical transceivers.]
Traditional MIL-C-38999 connector shell sizes and MIL- STD-1472 (Human Engineering) recommendations for connector spacing have conventionally driven the size of the connector panel and enclosure. Microminiature MIL-performance connectors provide the same or better physical, electromagnetic, and electrical performance as legacy “triple 9” connectors while providing higher-density contacts at roughly half the size and weight of traditional options. Consequently, there are now Ethernet switches and mission computers on the market today using these connectors that measure barely over one inch (around 3 cm) tall.
Also helping reduce SWaP in mission electronics for unmanned platforms is the shrinking of semiconductor die sizes and the addition of symmetric multicore processing (SMP) that boosts performance while reducing power consumption. Intel-based x86 processors use smart speed-stepping technologies to maximize performance, yet throttle back to save power when loads are lighter with the advantage of protecting the device from thermal damage.
Arm core processors similarly hone their own highly efficient power management capabilities in mobile devices. Further, Ethernet switch devices can now integrate advanced power-management technologies in the switch core and physical transceivers, such as Energy Efficient Ethernet (IEEE-802.3az) and ActiPhy, which put unused ports in a low-power idle mode, keeping links active but consuming less power during lower data activity. These switches can also sense the length of the cable connection, limiting power for transmitting data, to say, 10 meters (32.8 feet), rather than defaulting to the 100-meter (328-foot) Ethernet specification. In total, these technologies can result in cutting power consumption by 50% or more from traditional levels.
As manufacturers of SoC devices reduce the thermal needs of the silicon, they are also reducing the power-dissipation requirements on the system, which means a smaller surface area required for cooling of the chassis. The mechanical size of the enclosure can also be smaller thanks to higher density connector technology.
Innovative x86 and Arm-based processor technologies continue to integrate more capabilities into ever-higher density semiconductor packages with optimized power management. These low-power CPUs are frequently used in SoCs that include not only multicore microprocessors, but also advanced peripherals, such as a graphics processing unit (GPU), without the need for separate discrete components, helping to reduce overall SWaP for embedded electronics. Intel’s Atom processor is an example of an x86 SoC that integrates a lower-power quad-core CPU plus high-definition Intel graphics and I/O chipset in a single package, enabling the mission computer to have a very small 5.2 by 5.4 by1.4 inch (39 cubic inch) footprint and weigh less than 1.5 pounds while drawing less than 25 watts.
Because of the reduced instruction set nature of Arm architectures, Arm delivers superior million instructions per second (MIPS)-to-watt ratio with fewer transistors than processors based on complex instruction set computing (CISC) like x86 CPUs. Arm processors also reduce power consumption by operating at a lower clock frequency than x86 processors. In addition, Arm SoC vendors have integrated low-power states, such as power gating and clock gating, into their processors. Arm’s lower power design lends itself nicely to SWaP-constrained applications by providing a reduced thermal solution in a low-weight processor.
A rugged small-form-factor mission computer designed for military and civil tactical processing applications is the Parvus DuraCOR 8044 modular mission computer workstation. It features a sealed and fanless IP67-compliant design that enables system designers to meet compute-intensive requirements for applications deployed in the harshest environments. The ITAR-free, U.S. Commerce EAR-controlled unit features an 8-core, 16-thread, 11th-gen Intel Xeon W (Tiger Lake-H) processor. Designed to meet or exceed MIL-810G and DO-160G environmental test standards, the mission computer weighs 5.6 pounds and measures 6.75 by 6.25 by 3.5 inches (135 cubic inches). Its Intel Iris Xe GPU supports OpenGL for graphics-intensive applications and OpenCL for GPGPU-accelerated data processing-intensive applications. It also supports high-speed real-time Ethernet endpoint connectivity at rates up to 10 Gigabits for low-latency, on-time transfer of critical data. (Figure 2.)
[Figure 2 ǀ The Parvus DuraCOR 8044 is aimed at use in compute-intensive situations in harsh environments.]
The military and aerospace market maintains an insatiable appetite for smaller, lighter, and cheaper. As technology continues to advance, electronic device density and packaging improvements will continue to enable smaller and more cost-effective unmanned platforms. These factors will drive advancements in the SWaP optimization of rugged deployable small-form-factor mission computers and network solutions.
Jeff Evans has 20+ years in product management and serves as the Product Line Manager at Curtiss-Wright Defense Solutions for the Parvus DuraCOR, DuraNET and DuraMAR mission computers, switches, and routers.
Curtiss-Wright https://www.curtisswrightds.com/