Graphics processing - having it both ways
StoryJune 10, 2016
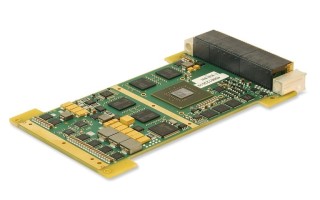
Military systems are noted for their high processing demands, a situation that is particularly true for graphics processing. Like their commercial counterparts, military displays are becoming faster, higher-resolution, and more complex. Both defense surveillance and commercial video-game applications, for example, share a need for the maximum possible raw graphics computational horsepower.
Military systems are noted for their high processing demands, a situation that is particularly true for graphics processing. Like their commercial counterparts, military displays are becoming faster, higher-resolution, and more complex. Both defense surveillance and commercial video-game applications, for example, share a need for the maximum possible raw graphics computational horsepower.
Driven by the consumer market, chip companies upgrade their products every year or two, sometimes delivering two times the performance per watt in successive generations. Board designers, in turn, use these chips to provide significant increases in performance per slot at their level in the food chain. We can be very thankful that the consumer-electronics industry yields to contractors the building blocks for national defense. Just think what it would cost otherwise.
Embedded graphics-processing units (GPUs) can perform both general-purpose computing and video and graphics generation, making them suitable for applications such as persistent wide-area surveillance; intelligence, surveillance, and reconnaissance (ISR); and radar or sonar processing. Even ground vehicles need specialized graphics processing in order to piece together a picture of the situation around them.
Designers of next-generation ISR systems, like designers of immersive video games, want the fastest, most massively parallel GPUs that the industry can provide. High-performance GPUs give defense system developers the throughput required to accomplish tasks such as sensor fusion, where data from different sensors is integrated into a whole that is greater than its individual parts; and video stitching, in which elements of a picture are sewn together to form a larger view.
Mil applications have unique needs
While they share with gamers a need for some of the same basic components, military applications also have a host of dissimilar requirements. For military users, backward compatibility is not just a “nice-to-have,” but an essential: New stuff still must talk to old stuff and built-in obsolescence is a fault, not a virtue. Perhaps more important, for military applications SWaP – size, weight, and power – is king. Thermal management, life cycle cost, and long-term support are also far more important in the military realm than in the commercial sphere.
So, while designers of ISR systems want the latest GPUs with hundreds of parallelizable processing units or cores – including single- and double-precision floating-point units – that’s just the start. Equally important is the accommodation of new as well as legacy video standards; form, fit, and function compatibility at the board, box, system, and platform levels; long-term logistics support; ease of upgradability; affordability and life cycle cost; and performance per watt. These factors carry different weights depending on the age of the platform, but none can be discounted. Flexibility is key.
A high-end GPU application might involve an airborne ISR system with multiple operators, where the chip simultaneously drives multiple displays, using multiple video standards. Or take a ground vehicle, where multiple sensors feed multiple displays, all with varying resolutions and formats, and with an even greater emphasis on SWaP and thermal management.
The same would be true of a sonar display on a submarine or a fire-control radar on a fighter aircraft, both of which need to minimize SWaP. The best graphics solution for these must provide not only optimal SWaP trades but also the most flexible processing and video-output technology.
All of these applications need to process a lot of sensor data quickly and efficiently. High-performance GPUs provide the throughput required to accomplish sensor fusion and video stitching. Moreover, graphics chips that include double-precision floating-point hardware minimize the impact of artifacts introduced by single-precision processing.
An example of such a backward-compatible graphics processing board is Abaco Systems’ rugged GRA113 3U VPX product with NVIDIA’s 640-core GPU, which features configurable video outputs to accommodate multiple resolutions, aspect ratios, and legacy displays. (See Figure 1.)
The performance curve of the semiconductor industry – propelled by the demands of the consumer electronics market – is a gift that keeps on giving. Continuous upgrades and performance increases make it possible for board designers to do more with less – exploiting greater throughput in the same volume, while potentially lowering life cycle costs.
Figure 1: The Abaco Systems GRA113 3U VPX rug-ged high-performance graphics board features a 640-core GPU from NVIDIA.
(Click graphic to zoom by 1.9x)
www.abaco.com