Versatility is key as OpenVPX enclosure requirements continue to evolve
StoryFebruary 10, 2021
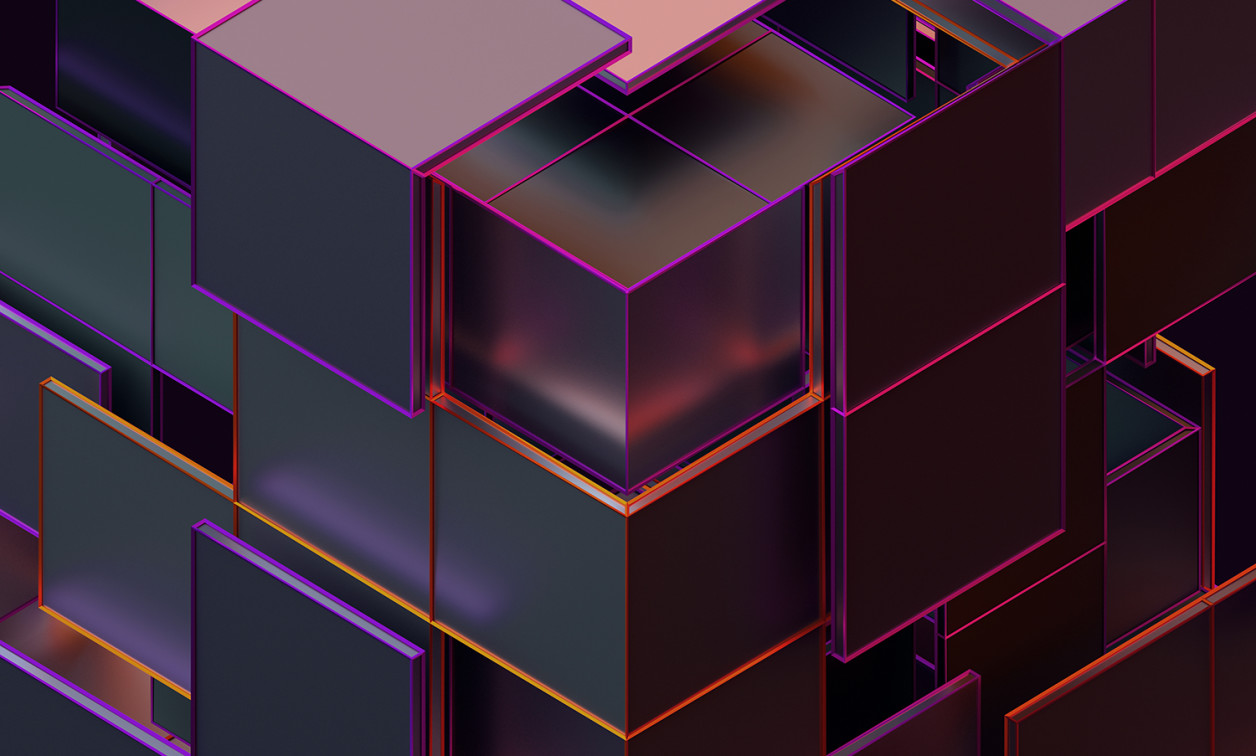
Despite the fact that OpenVPX is an open standard architecture, there is a significant amount of variation of system platforms. The application needs for OpenVPX systems continue to evolve rapidly. New challenges brought by the SOSA [Sensor Open Systems Architecture] Consortium’s efforts; new complementary VITA [VMEbus International Trade Association] standards; size, weight, and power (SWaP) concerns; the expanding number of backplane profiles; and SpaceVPX implementations are requiring a versatile approach by the backplane/enclosure developers.
Being an OpenVPX backplane developer can be maddening: Even with established VITA 65 profiles, there are so many variations that it can be very challenging to develop a standard backplane. Once upon a time, backplane design was largely a factor of the architecture and its form factor (3U or 6U) and the number of slots. With OpenVPX, in contrast, there are dozens of VITA 65 routing profiles that all have their own signal definitions. In recent years, the ability to add optical (VITA 66.x) and RF (VITA 67.x) housings on the backplanes creates a wide variety of new configurations to the list of profiles. There are various subsets of the VITA 66 (.1, .2, .3, .4, .5) and VITA 67 housings (.1, .2, .3a, .3b, .3c, .3d) as of this writing, most of which require differences in the backplane design. Complicating all of this is that fact of the possibility of different slot pitches. The 1.0-inch is typical for a backplane, but 0.8 inch is not unheard of, and wider than 1.0-inch pitch is no longer a rarity.
The SOSA [Sensor Open Systems Architecture] Consortium’s efforts have brought timing/clocking protocols to the backplane, which adds another factor of differentiation to designs. Of course, the backplane speed requirement can change the stack-up of your routing, back-drilling, and PCB [printed circuit board] materials that you use. Therefore, the speed of the backplane is yet another factor that can prevent standardization. With speeds hitting PCIe Gen4 (~16 Gb/sec) and 100 GbE (4 lanes of ~25 Gb/sec), the performance challenges are increasing. Housings or cutouts for the VITA 66/67 contacts limits space for routing, particularly when the design is a 3U and a larger slot count.
So, you can imagine the number of options for an OpenVPX backplane design. There are slots (approximately 10 common slot sizes), profile options (average of about three for each common slot size), 3U or 6U, VITA 66/67 options (about five common versions between them), speeds (three common speed tiers), how many slots have VITA 66/67 cutouts/housings (15 common configurations), and more. This would require 10/3/2/5/3/15 backplane designs just to get some common designs laid out, not even accounting for any custom routing, specialty I/O requirements, VITA 62 PSU [power supply unit] slots, specialty slot pitches, etc.
With the increased use of VITA 66/67 housings, there are a few configurations that can help make the options more manageable. This first is an 8-slot 3U OpenVPX backplane with 4x VPX power and ground-only slots and 4x VITA 67.3/VITA 66.5 cutouts. (Thankfully, the VITA 66.5 folks devised a way to use the same VITA 67.3 cutouts on the backplane.) With SOSA clocking, the backplane provides versatility for development systems. Single-slot power and ground backplanes with either VITA 66 or VITA 67 also provide flexibility in design; these can be added to a standard backplane profile configuration to expand the options. In some development systems, it is desirable to have VITA 62 slots. These can be offered in standalone single-slot power interface boards or as part of an overall backplane. For development, a version with four VPX slots, two VITA 67.3 slots, and dual VITA 62 PSU slots offers further versatility. Figure 1 shows a variation of these VITA 66/67 configurations.
[Figure 1 | Development backplanes can offer versatile configuration options to address the various OpenVPX, VITA 66 (optical), and VITA 67 (RF) implementations.]
Chassis mechanicals – even more options
There exist so many possible iterations of OpenVPX backplane options, plus the many chassis options don’t make things any easier. However, there are more ways to enable modularity in the enclosure. First, the application will help dictate the type of enclosure. One example: Is a commercial rackmount or desktop required or is it a deployed unit? Some OpenVPX applications are used in a benign environment, often in a data center or ground communications hub. The advantage of the 19-inch rackmount is that it’s ideal for prototyping/development and can often be used in the applications that do not require military-level ruggedization. A designer can also start with a commercial-grade version for development and go to a rugged rackmount in deployment. As seen with the backplanes, there are a lot of options: various slot pitches (0.8, 1.0, 1.2 inch, etc.), 3U versus 6U boards, various cooling methods, and more.
SOSA-based systems typically use high-power boards along with VITA 66 for optical and/or VITA 67 for RF contacts. It is common for multiple slots to be more than 100 watts each. High slot counts can create the need for a system that can dissipate a high amount of heat. Larger chassis can implement high-CFM fans that pull the air from below the card cage and blow the heat 90 degrees out the rear of the system. This setup enables rear-transition modules (RTMs) to be plugged in all of the slots in the rear of the enclosure, maximizing density for testing or deployment. The capability to handle the RF/optical cabling and any RTM or VPX cabling interfaces in this type of front-to-rear cooled chassis is important for SOSA systems. The chassis can cool at least 2000 W in the 6U size (for 3U OpenVPX boards), but with a taller enclosure can cool even more.
6U OpenVPX boards can also be placed in a 9U tall chassis, even possibly with a divider plate to split the enclosure into two rows of 3U slots. Alternatively, the designer can employ a hybrid solution with a mix of 3U slots and 6U slots. Rather than using a chassis where the boards are mounted vertically, horizontally plugged-in boards can save rack space. Usually these systems only use between two and eight slots.
To maximize versatility in any of these designs, it is important to have flexibility in the type of card guides and their position. As noted, the pitch of some slots may be wider than others. Therefore, having the ability to space the slots as needed with specialized card guides is a huge benefit. This situation might include the use of card guides for conduction-cooled boards, which may be used alongside card guides for air-cooled boards.
SOSA is also shifting the chassis power to 12 V heavy systems. A modular fixed PSU enables users to select the submodules of 3.3 V, 5 V, 12 V, and AUX voltages that may be required for all types of OpenVPX applications. With the RF/optical options, there is typically the need to provide more I/O and cabling options to the rear of the chassis. Using an enclosure with fans above the card cage allows for plenty of space for the rear I/O cabling or RTMs in the system. Further, SOSA is leveraging the use of VITA 46.11 system management, which means that the chassis is able to monitor the slots, voltages, and fans.
Worlds colliding
SpaceVPX brings new challenges as it supports the use of both 160 mm and 220 mm deep boards. Further, the pitch of the modules is often wider, at a 1.2 inch board width. To enable more versatility for SpaceVPX, a dual-depth OpenVPX test/development chassis can be utilized. (Figure 2.) To support the various types, the enclosure needs to support both the 160 mm and 220 mm depth boards, a 1.0 and 1.2 inch pitch, etc. Special card guides for the 1.2 inch pitch needed to be created in both the depths for conduction-cooled boards.
[Figure 2 | SpaceVPX uses both 160 mm and 220 mm depth OpenVPX boards as well as wider spacing options. A dual-depth chassis provides the ability to test the various card sizes/pitches in the same enclosure.]
One of the benefits in working with the special form factor requirements for SpaceVPX is the smoother transition to supporting extra-deep modules and/or wider boards. Engineers at several of the RF-centric defense contractors are packing more punch into each module. As a result, in some applications the boards are getting longer or wider. These hybrid OpenVPX systems require enclosure card cages that can support these sizes and properly cool them. Figure 3 shows a military-spec rugged 19-inch rackmount chassis platform for customized OpenVPX supporting wider and deeper boards. To support the heavier cards, an extra-rugged milled card-guide tray and other elements ensure that the unit can meet the shock and vibration requirements of the application. Although this design had nothing to do with SpaceVPX, having that experience and the specialty components helped leverage a solution for another OpenVPX application.
[Figure 3 | Designers can leverage the OpenVPX standard for specialty designs. This military-spec rugged enclosure shows an example with extra-deep 6U boards and a wider pitch.]
Other space-saving options
It is certainly possible to use a horizontal-mount enclosure to save rack space and weight. Typically, these enclosures would be for smaller systems, namely six or fewer slots or less for 6U boards and eight or fewer slots for 3U boards. With the boards mounted side by side, a 6U board will fit next to a 3U board in the same slot row. Therefore, it is easy to mix and match both 6U and 3U boards. The 3U option also includes the possibility of using pluggable VITA 62 PSUs. Alternatively, there are modular fixed PSUs that can go above the card cage.
For example, a 3U tall horizontal-mount enclosure can support five OpenVPX boards in the 6U height and four 3U OpenVPX boards along with a pluggable VITA 62 PSU (all at one-inch pitch). It is possible to have various levels of ruggedization for these types of enclosures.
ATRs and cooling options
SOSA and VITA 66/67 implementations in ATR format require adequate spacing beneath or behind the backplane for the cabling bend radii. Therefore, many of the legacy ATRs in the market cannot support those requirements without some redesign. One solution that gets around that issue is a front- or rear-loaded ATR. With the cards sliding in horizontally into the rear of the enclosure, there is space behind the backplane to cable around to the front of the chassis or to the back panel. Figure 4 is an example version with three OpenVPX slots and one VITA 62 PSU slot.
[Figure 4 | A front-or rear loaded ½ ATR for 3U OpenVPX can easily allow both standard OpenVPX modules or versions with VITA 66/67 interfaces in a compact design.]
For a top-loaded ATR, there can be a standoff for the VITA 66/67 contacts to allow for the cabling to go through. As SOSA-based systems tend to have very high power, there are now cooling conventions to achieve the heat dissipation needed for 125 watt to 185 watt OpenVPX boards in the wedge-lock format. Cooling a 185 watt board is achievable with air in the air-cooled board format (without wedge-lock casings). Enough airflow can be directed to have the airflow pass directly over the chip sets. When the card is encased in a conduction-cooled format with wedgelocks, the air can pass over the board, but much of the airflow is blocked by the structure of the card. The size and shape of a typical conduction-cooled board acts as a giant airflow blocker.
With optimized spacing between the modules and using airflow baffle to optimize the air paths, simulation has shown that these boards can be cooled in a commercial forced-air enclosure. For a system requiring military-specified fans, this aspect becomes extremely difficult. The VITA 48.7 standard has the potential to resolve this issue for many of the high-wattage boards in the market, as the specification provides channels on the conduction-cooled modules for the air to flow directly over and through the heat sink fins. This approach will certainly help improve the cooling for those modules For the hottest level of boards, a liquid-cooled enclosure would be required.
A versatile world
Designers of military and aerospace solutions can look to OpenVPX for a rich and diverse ecosystem for leading-edge C5ISR [command, control, communications, computers, combat systems, intelligence, surveillance, and reconnaissance] applications. As the requirements get more complex, providing versatile designs that can be used in a wide range of applications is a key to success.
Justin Moll is vice president, sales and marketing, at Pixus Technologies. He has been a sales and marketing management consultant and senior-level manager for embedded computing companies for more than 20 years. Justin has led various committees in the open standards community and is a regular guest speaker at several industry events. He holds a degree in business administration from University of California, Riverside. Readers may reach the author at [email protected].
Pixus Technologies https://pixustechnologies.com