Military power conversion: the value of strategic customization (Part 1)
BlogMarch 30, 2020
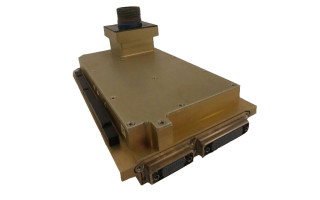
As the military-electronics industry continues to transition toward commercial off-the-shelf (COTS) products, established standards, and modular designs, the need for tailored solutions remains – there is a middle ground. In this, Part 1 of a two-part blog series, the benefits and drawbacks of custom parts are discussed.
Program managers and acquisition professionals supporting the Department of Defense (DoD) have long sought to drive down cost and schedule risks. One of the simplest ways to achieve this goal is by using components and subsystems conforming to well-established industry standards. The trend of increased standardization holds true in the power conversion market with the growing adoption of both physical and electrical industry standards, such as VITA 62, VITA 46, and MIL-STD-1275, among others.
However, there is a fly in that ointment: The benefits of well-defined design standards come at the cost of a reduced capability to tailor and customize power supply solutions to meet the unique performance requirements prevalent in military systems.
Rugged power supplies capable of addressing unique industry challenges have become a critical design element in today’s military electronics. Mature standards such as MIL-STD-704 and MIL-STD-1275, defining electrical power characteristics; or MIL-STD-461, characterizing electromagnetic compatibility (EMC) characteristics, have standardized best-design practices for engineers.
Meanwhile, budget constraints have forced program managers to seek commercial off-the-shelf (COTS) parts for modular, open architecture solutions to address onerous challenges on behalf of our warfighters. The DoD has distributed its intent to acquire hardware solutions that comply with modular open systems architecture (MOSA) standards to support rapid upgrades of technology, address obsolescence, and ensure interoperability between systems.
The VPX form factor has quickly become a design tool engineers leverage to address many of the above standardization challenges, all while improving performance. The standardization of mechanical and electrical features has resulted in VPX products viewed as a commodity. However, the benefits of standardization may continue to be outweighed by the challenging performance requirements engineers face. Output voltages, load current limit levels, stable responses to significant load step, EMC, inrush current surge limitation, and telemetry communication are some of the critical elements of a power supply integrated to a military system. Possessing the ability to customize these, and many other features of a power supply, even within a standardized mechanical form factor, remains an important capability to the design engineering, systems engineering, and testing community.
To many, customization is a scary word, suggesting increased cost, schedule slips, or increased technical risk. In reality, customization can actually reduce cost and schedule. A power supply manufacturer who can support tailoring of key features may be a designer’s ally, especially when designing from an existing, field-proven, baseline product with little or no nonrecurring engineering (NRE) costs and rapid prototyping capabilities. This is especially true with an aging workforce specializing in power electronics.
Many COTS ruggedized or military-grade VPX products exist today, built to comply with some or all of the following: VITA 46 mechanical and VITA 62 electrical specifications, as well as MIL-STD-461 (EMC), MIL-STD-704 (aircraft electric power), MIL-STD-1275 (military vehicle electric power), and MIL-STD-810 (environmental conditions); these comprise standards establishing the minimum criteria for any power supply implemented in a defense application.
In Part 2 of this blog, we’ll discuss several examples of what we call strategic customization, as parts built to comply with baseline configurations are not capable of addressing every unique specification.
Mike Eyre is Global Marketing Manager at Milpower Source in Belmont, New Hampshire.
Milpower Source · https://milpower.com/