3D printing and rugged single-board computers
BlogJuly 31, 2017
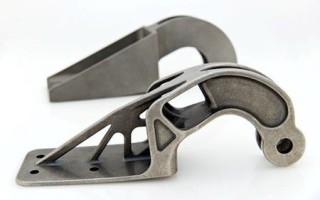
Additive manufacturing, and more specifically metal additive manufacturing (or metal 3D printing), is changing the manufacturing industry by lifting some of the design constraints inherent to traditional processes. Many industries are benefitting from this technology including the defense electronics world, where lattice structures have been applied to single-board computer (SBCs) assemblies to reduce weight while maintain performance and ruggedization requirements.
The additive manufacturing process creates parts layer-by-layer as opposed to removing material by computer numerically controlled (CNC) operations. Metal additive manufacturing is used in the production of critical aerospace components such as rocket engines or commercial aircraft structures, offering a clear advantage in terms of weight reduction. Aluminum and titanium, among other metals, can be printed with high accuracy and repeatability into complex shapes, as seen on Figure 1.
A VITA 48.2 conduction-cooled SBC main components –a circuit card with its connectors and components – are sandwiched between a primary and secondary cover. The covers, made of machined aluminum, provide a mechanical interface to the chassis via wedge-lock systems, flexural stiffness to avoid components vibration fatigue failure, and heat sink functions to lower the components operating temperature. Both the primary and secondary covers, because of their massive nature, are perfect candidates for an additive manufacturing process, with the main goal being to decrease mass while maintaining comparable performance structurally and thermally.
Lattice structures
Another key part to this process would be to leverage geodetic and lattice structures. A geodetic or lattice structure is a type of design that uses many closely spaced diagonal truss elements to provide structural integrity without the weight penalty of a massive construction.
Sir Barnes Wallis pioneered geodetic structures in aircraft design in the 1930s. The Vickers Wellington bomber had lattice structures that could take incredible damage without breaking, while providing weight savings of 40 percent or more. High assembly cost and complexity made it impractical for high volume production as required during wartime.
With current metal additive manufacturing processes, fabricating lattice structures is now an easy and fast process that can be applied to many different types of structures as seen on Figure 2, bringing the same beneficial stiffness/weight ratio.
[caption id="" align="alignnone" width="450" caption="Figure 2: Pictured are examples of lattice designs. Image courtesy of TEN TECH LLC."][/caption]
The goal of a lattice core design will be to lower the weight of the cover, which in our example weights 2.25 pounds, while maintaining structural and thermal performance comparable to the standard design. To comply with interface requirements and VITA 48.2 constraints, the design maintains all external features of a standard primary cover, but uses a hollow/lattice core as shown in the cross section in Figure 3.
[caption id="" align="alignnone" width="450" caption="Figure 3: Pictured is a lattice cross section. Image courtesy of TEN TECH LLC."][/caption]
The tetrahedral pattern lattice structure is defined using a proprietary algorithm TEN TECH LLC designed to evenly distribute lattice beams and allowing for density variations based on geometric curvature tolerance or stiffness requirement. The face sheet thickness is chosen to provide enough support and thermal mass to the structure. Thermal sinks for the main components as well as screw bosses are passing directly through the Lattice core and provide stiffness and/or thermal mass where needed.
Results
With this design, we can achieve close to 50 percent mass reduction: the new primary cover weighs in at 1.23-pounds, about a 1-pound weight saving. We also saw a 40 percent weight reduction over a standard VITA 48.2 design. A 2-pound weight reduction per SBC could bring a five to 20 pound overall system weight reduction. Also, the first natural frequency is high enough to avoid dynamics coupling with chassis and equipment, with natural frequencies comparable to the VITA 48.2 cover within MIL-STD-810 range of interest for sine and random vibration. We noticed that despite a slightly higher temperature concentration, the lattice cover enables sufficient dissipation of the components heat, thanks to the through-core protrusions.
This phase I study focused on the feasibility of an original lattice design, which was proven by simulation. The phase II study will focus on development and prototyping, to enable a repeatable and predictable product capable taking the place of a standard VITA 48.2 component. Even if it was applied to a 6U VITA 48.2 primary cover, the lattice core design can be easily applied to 3U payloads and even chassis substructures, essentially replacing massive machined aluminum plates with a much lighter lattice design.
For more information and data on this process, visit www.tentechllc.com and our whitepaper on this topic at https://www.tentechllc.com/resources/Metal-AM-for-VITA-48.2-SBC.pdf.