Rugged networking on the move: Best practices for design and test for constrained-space applications
StoryNovember 29, 2017
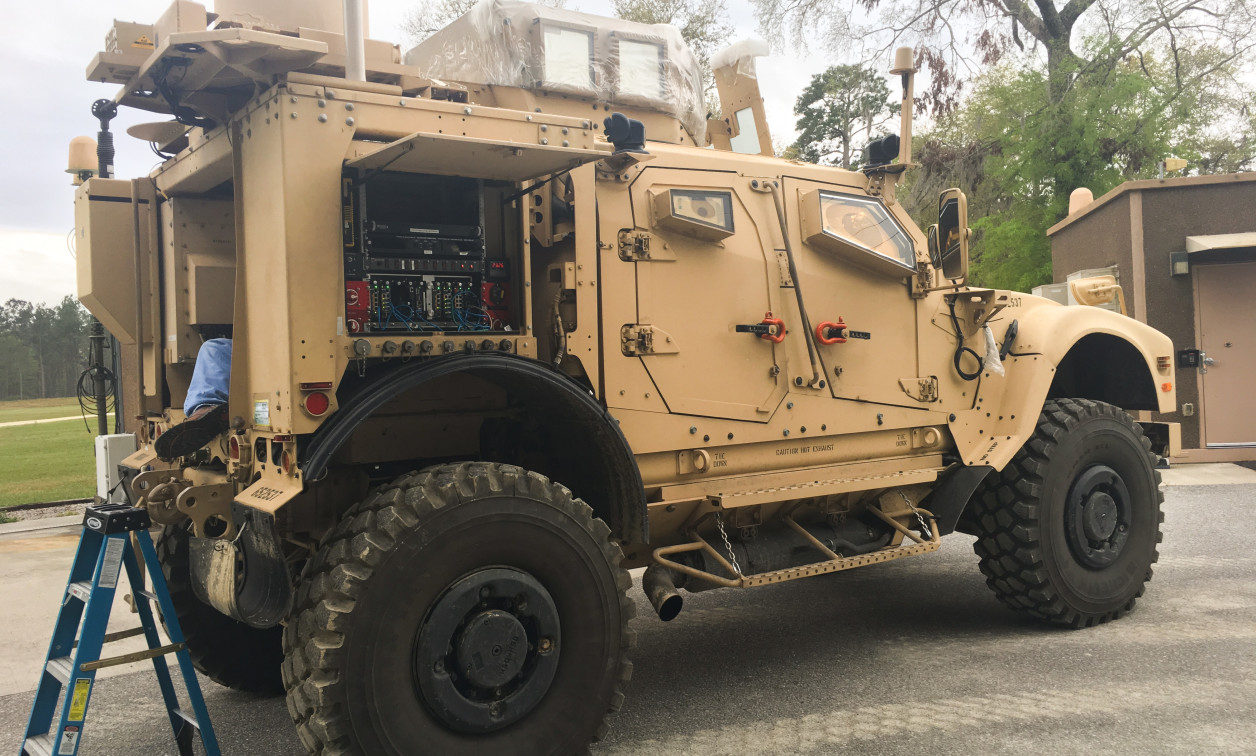
In the unpredictable environment of the battlefield, the fight does not stop just because you are moving. That reality puts and it's warfighters at a distinct disadvantage if they cannot maintain situational awareness at all times.
As adversaries equip themselves with the latest wireless technology and smartphones while actively moving in ground vehicles. Mobile Internet Protocol (IP) networking is a necessary response by the Department of Defense (DoD) to counter the many foes, who have ready access to this ever-smaller mobile technology.
To maintain information dominance, warfighters across all branches of the military require networking-on-the-move to stay on top of complex threat environments.
The DoD’s moves are enabling U.S. warfighters to be more agile and prepared. For instance, the U.S. Marine Corps NOTM Increment 1 (Inc1) Refresh program is an integrated tactical mobile network working to leverage proven commercial and government technology to expand and enhance communications capabilities. Combat vehicles integrated with networking-on-the-move equipment provide reliable communications, mission command, and situational awareness from anywhere on the battlefield, even in the most remote environments and challenging terrains.
Ability to handle rugged terrain
When traversing rugged terrain, military vehicles can experience a high level of shock and vibration. Networking-on-the-move systems must be able to stand up to that abuse so that communications are not interrupted.
In the past, methods to deploy access to tactical networks have included commercial off-the-shelf (COTS) equipment originally designed for data-center environments. A new generation of ruggedized COTS equipment is now available that makes mobile battlefield networking more reliable, while continuing to maintain interoperability with enterprise networking equipment, thereby ensuring end-to-end communications.
Address full mobility needs in constrained spaces
Mobility ultimately drives networking-on-the-move, but the amount of available real estate within ground vehicles, aircraft, and ships does not change. Along with increased demands on communications systems to provide more capability (such as Wi-Fi or LTE) and more cybersecurity in the field comes the inevitable side effect: Networked systems consume more space.
As a result, full mobility demands innovation and modernization designed to reduce size, weight, and power (SWaP) requirements. In this realm – with all other things being equal – communications equipment can never be too small, too light, or too power-efficient.
Reliability in challenging vehicle environments
Products intended for mobile battlefield use must meet high standards of environmental testing for shock, vibration, and temperature. Requirements for ground vehicles are stringent; conditions are even more stringent for aircraft, because ill-designed or poorly manufactured communications equipment can put the aircraft and warfighters at great risk. Compliance with third -party testing to MIL-STD-810G and MIL-STD-461F are critical to assure reliably in actual operations in remote or mission-critical settings. These standards are increasingly relevant as DoD increases adoption of COTS technologies in lieu of purpose-built military-only products in order to benefit from the commercial world’s rapid pace of technology advancement and cost-saving economies of scale.
What to look for in vendors’ design and test best practices of vendors
Adapting sensitive, high-performance electronics to withstand conditions found on the network’s edge – regardless of industry or application – is no easy task. This reality has led to development of compact rugged network modules designed and manufactured by specialized vendors. These modules typically use COTS equipment and networking software from industry-leading manufacturers, which makes it easy to securely connect to enterprise networks. SHowever, starting with enterprise-class technology is just the beginning, however.
Optimized chassis design
The heart of any rugged module is its chassis. The best designs for optimizing SWaP use a variety of materials and design processes, including machined heat sinks and heat-spreader plates using aluminum and copper for efficient heat transfer, machined steel for critical structural elements, sheet metal for electromagnetic (EMI) protection and plastics and composites for weight savings.
Once designed, the modules should be tested to validate the design. To be certain that rugged equipment will hold up, the best designers follow a regimented test methodology with calibrated, certified, independent test labs – and can make complete and extensive test documents available. To save costs, some vendors will perform their own testing in-house, with some not completing the full range of tests. Some vendors only go as far as claiming their systems are “designed to meet” standards, but do no testing at all. For ultimate confidence, independent testing is an expensive, but necessary step. Once constructed, the system should be tested to make sure that it adheres to standards, under real-world conditions.
Conductively cooled
Since rugged equipment must be able to withstand dust and sand, the traditional method of using cooling fans to drive airflow through the equipment enclosure is not an option. In such conditions, other methods must be used to cool systems, since heat is the mortal enemy of electronics. In a fanless design, efficient heat transfer is vital to ensuring durability. The chassis plays a vital role in dissipating heat – it must be designed with careful attention to optimal heat transfer from critical electronic components on the embedded circuit boards and power supplies. Once designed, the modules can be tested for operations in heat/cold extremes in independent labs.
Protected and reliable power systems
Another environmental challenge faced by rugged systems includes poor quality and unreliable power sources – especially for equipment mounted on vehicles, running on generators, or deployed overseas in countries with poor quality power. DC power systems can provide power that is inconsistent in voltage, intermittent, and noisy.. These problems can be caused by other devices attached the power sources as well. Additional problems can crop up due to user error such as connecting DC power wires backwards, or by short circuits.
To offset these problems, power supplies must be designed to accept the widest possible range of input voltage (for example, 10 V to 36 V), should be reverse-voltage and short-circuit protected, and should include extensive filters and capacitors to maintain a clean, reliable source of power to internal components. One recent innovation to look for in best-of-class AC power supplies is the use of single-stage AC to DC conversion, which provides higher efficiency, less power loss, and less dissipated heat. These technologies are also smaller in size than traditional two-stage converters and will perform at lower temperature ranges.
Eliminating eiEMI
Networking equipment mounted in vehicles typically resides in environments shared with many other computers and radios; some may be mounted near radar equipment. In such setups, it’s paramount that all of the onboard equipment is designed and tested to ensure it does not cause, and is not susceptible to, – EMI, to ensure reliable performance of the equipment and ensure that the equipment does not cause neighboring equipment failure.
EMI occurs in the form of both unintended radio “over-the-air” interference, and conducted interference through power and data connections; both kinds must be mimimized through shielding and filtering. In networking equipment, typical sources of issue are the power supplies. For defense applications, the standard MIL-STD 461 is used to test for EMI, including radiated and conducted emissions and susceptibility. This standard is roughly 10 times more stringent than typical FCC standards used for data center and consumer equipment. Because the military standard is so strict, small issues in design and manufacturing can cause systems to fail this test.
100 percent tested in manufacturing
Such stringent testing can be conducted only on a limited number of units, since it’s extraordinarily expensive and time-consuming; what’s more, the equipment subjected to those tests can’t be shipped to customers as “new.” However, newly manufactured equipment must be tested throughout the manufacturing process to ensure that the new equipment conforms to design specifications.
Certain types of environmental stress screening (ESS) testing can be conducted safely and efficiently on all new units, ensuring that common failures are identified before ever leaving the factory. The failure rate in this step tends to be about five percent. five ESS screening is, to be fair, expensive and time-consuming, but if vendors skimp on stress testing the risk of failure is merely passed on to designers and users..
Real-world tested
While laboratory testing is critical to ensure that test coverage is complete, standardized, and quantifiable, real-world testing also plays a critical role in assessing performance and reliability – exposing equipment to deployment-specific environmental factors that are hard to anticipate and reproduce in a lab.
Moreover, in addition to environmental factors, real-world testing can expose opportunities to improve usability, accessibility, and maintainability – along with gathering observations from end users and operators. Real-world testing also provides designers and programs with confidence that complete systems actually work together as intended.
Designing, testing, and manufacturing rugged, reliable networking equipment is time-consuming, expensive, and detail-oriented. Requiring effective test processes of vendors when selecting networking equipment means that the DoD can ensure that its warfighters can meet any threat.
Charlie Kawasaki joined PacStar in early 2005 to lead the company’s technology strategy and future product roadmap for its proprietary product lines. He holds extensive experience in product development, software engineering, technology licensing, patent development, business development, product marketing, general management and M&A.